Top ten considerations for drilling rig maintenance;
In the maintenance work of special vehicles, there are some common and easily overlooked wrong practices. These actions may have a negative impact on the vehicle’s performance and even seriously affect its service life. The following details ten taboos in the maintenance of drilling rig special vehicles:
Taboo 1: Only adding engine oil without changing it
Engine oil plays multiple important roles such as lubrication, cooling, and cleaning in the operation of a diesel engine. Many drivers pay attention to checking the oil level and add oil according to the standard, but often ignore the quality of the oil and the timely replacement of the deteriorated oil.
During normal use, the consumption of engine oil is relatively small, but it is easily contaminated. During the operation of the diesel engine, many contaminants, such as carbon smoke, carbon deposits, and scale generated by incomplete combustion of fuel, will mix into the oil. For new or overhauled machinery, there will be more impurities after the test run. If you simply add oil without changing it and put the vehicle into use, it is very likely to cause unexpected failures such as burnt bearings and seized shafts.
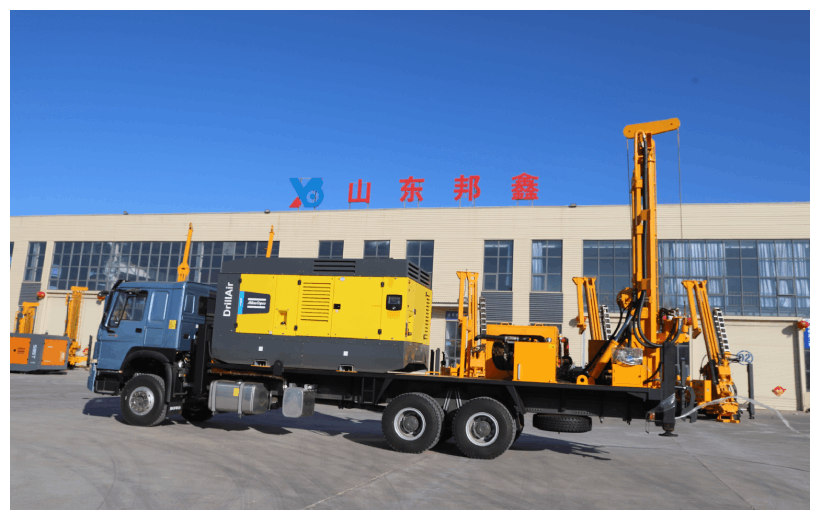
Drilling rig truck
In addition, even when changing the engine oil, some drivers, due to lack of relevant maintenance experience or for the sake of convenience, do not thoroughly clean the oil passages. As a result, mechanical impurities will still remain in the oil pan and oil passages, failing to ensure the normal circulation of the oil and good lubrication of the machinery.
Taboo 2: Misusing and over – applying grease
Applying grease on the cylinder head gasket
Grease is a commonly used lubricant in the repair of construction machinery, with lubrication and sealing functions. Some repairmen apply a layer of grease on the cylinder head gasket when installing it, thinking that it can enhance the sealing performance of the diesel engine. However, this practice actually affects the working performance of the diesel engine.
The cylinder head gasket is a key sealing part connecting the diesel engine block and the cylinder head. It not only has to seal the high – temperature and high – pressure gas in the cylinder but also ensure that the cooling water and lubricating oil in the cylinder head and the engine block do not penetrate each other. When disassembling and installing the cylinder head gasket, the requirement for sealing quality is extremely high. If grease is applied to the cylinder head gasket during installation, when the cylinder head bolts are tightened, part of the grease will be squeezed into the cylinder water passages and oil passages. The grease remaining between the gaskets will, under the high – temperature environment of the cylinder operation, partly flow into the cylinder for combustion and partly remain on the joint surface between the cylinder block and the cylinder head, forming gaps. Haut – temperature and high – pressure gas can easily impact the cylinder head gasket from here, causing the gasket to be damaged and resulting in air leakage. Moreover, the grease will produce carbon deposits after being in a high – temperature state for a long time, causing the cylinder head gasket to age and deteriorate prematurely. Therefore, never apply grease when installing the cylinder head gasket.
Applying grease on tire nuts
Many repairmen apply grease on the bolts and nuts of tires to facilitate tightening the nuts and prevent them from rusting, which is actually a wrong practice. After the tire nuts are tightened, the threads form a self – locking characteristic because the helix angle of the thread is smaller than the equivalent friction angle between the threads. In actual bolt connections, the helix angle is fixed, while the equivalent friction angle changes according to the friction state between the threads. If oil is applied to the nuts and bolts, the equivalent friction angle between the threads will decrease, making the self – locking performance of the bolt connection worse and the nuts more likely to loosen, which may cause serious safety problems.
Taboo 3: Installing new cylinder liners and pistons without matching
When replacing cylinder liners and pistons, many people think that new cylinder liners and pistons are standard parts with good interchangeability, so they directly install them after purchase. However, the dimensions of cylinder liners and pistons all have a certain tolerance range. If you carelessly match the largest – sized cylinder liner with the smallest – sized piston and install them, it will result in an excessive clearance between them. This will lead to problems such as weak engine compression and difficult starting.
Therefore, when replacing cylinder liners and pistons, you must carefully check the size grouping codes of standard cylinder liners and pistons to ensure that the installed cylinder liners and pistons have the same grouping code, so as to ensure a standard matching clearance between them. In addition, even for cylinder liners and pistons with the same grouping code, the cylinder – piston clearance should still be detected before installation in each cylinder to prevent the installation of counterfeit and inferior defective products.
Taboo 4: Not checking the plunger stroke margin
During the debugging of the plunger – type fuel injection pump, some maintenance personnel easily ignore the check of the plunger stroke margin. The plunger stroke margin refers to the distance that the plunger can continue to move upward after being pushed to the top dead center by the cam on the camshaft.
After adjusting the fuel supply start time, checking the stroke margin is to further confirm the wear condition of the plunger and the sleeve. After long – term wear of the plunger and the sleeve, the plunger needs to move upward a longer distance to start fuel supply, which will delay the fuel supply start time. When the adjusting bolt is unscrewed or a thicker adjusting pad or shim is used, the lowest position of the plunger moves upward, resulting in a reduction of the plunger stroke margin.
Therefore, when maintaining and debugging the fuel injection pump, the stroke margin should be checked first to determine whether the fuel injection pump still allows further adjustment. Usually, there are two checking methods:
a) Rotate the camshaft to push the plunger to the top dead center, then remove the delivery valve and its seat, and measure with a depth vernier caliper.
b) After the plunger is pushed to the top dead center, use a screwdriver to pry up the spring seat of the plunger spring to make the plunger rise to the highest position. Then use a feeler gauge to measure the gap between the lower plane of the plunger and the adjusting bolt of the tappet. Generally, the standard stroke margin of the plunger is about 1.5mm, and the limit stroke margin after wear should not be less than 0.5mm.
Taboo 5: Inaccurate measurement of cylinder clearance
When measuring the cylinder clearance, it should be measured strictly in the direction perpendicular to the piston pin hole at the piston skirt, not in other directions. The aluminum alloy piston has distinct structural characteristics, being smaller at the top and larger at the bottom, presenting a cone shape, and its local cross – section is oval. Therefore, the cylinder clearance along the circumferential direction is not completely the same.
To ensure the accuracy of measurement and the convenience of operation, it is stipulated that the clearance in the direction of the long axis of the ellipse should be used as the standard, that is, the measurement should be carried out in the direction perpendicular to the piston pin hole at the piston skirt. During the actual working process, the direction perpendicular to the piston pin hole at the piston skirt is subject to lateral pressure and has a greater degree of wear. Therefore, measuring in this direction can more accurately reflect the real situation of the cylinder clearance.
Taboo 6: Heating the piston with an open flame
The piston and the piston pin have an interference fit. When installing the piston pin, the piston needs to be heated to expand. However, many maintenance personnel use the method of directly heating the piston on an open flame, which is completely wrong. Because the thickness of each part of the piston is uneven, the degree of thermal expansion is also different. Heating the piston with an open flame will make the piston heat unevenly, easily causing deformation problems.
At the same time, carbon ash will adhere to the piston surface during the open – flame heating process, which will reduce the service life of the piston. If the piston cools naturally after reaching a certain temperature, its internal metallographic structure will also be damaged, greatly reducing its wear – resistance and significantly shortening the service life of the piston. The correct method is to heat the piston evenly in hot oil to make it expand slowly.
Taboo 7: Polishing the bearing shell with sandpaper
For some maintenance personnel with insufficient experience, the processing of bearing shells is a difficult task because the scraping technology of bearing shells is not easy to master and it is difficult to meet the ideal technical requirements. To increase the contact area between the bearing shell and the crankshaft, some people choose to use sandpaper to polish the bearing shell instead of scraping, which is not allowed in actual maintenance.
The abrasive grains on sandpaper are relatively hard, while the bearing shell alloy material is relatively soft. During the polishing process, the sand grains are easily embedded in the alloy material. When the diesel engine is working, this will accelerate the wear of the journal, shorten the service life of the crankshaft, and may cause relatively serious mechanical failures.
Taboo 8: Over – tightening the bolts
During the disassembly and assembly of construction machinery, the bolts installed in many parts have specified torque requirements. For example, for parts such as the transmission box, cylinder head, tires, connecting rods, and front axle, the tightening torques of the bolts in these parts are clearly specified in the product manual. Maintenance and users should not change these requirements at will.
Some users mistakenly think that the greater the tightening torque, the safer the bolts. However, over – tightening will cause many problems. Excessive tightening torque may break the screws or bolts and may also cause the threads to slip, resulting in mechanical failures, increasing maintenance costs and safety hazards.
Taboo 9: Over – inflating the tires
The inflation pressure of the tires of wheeled construction machinery has an important impact on its service life and work efficiency. Over – inflating or under – inflating the tires will shorten their service life to a certain extent and is not conducive to the safe driving of the vehicle, especially in hot summers.
The scientifically reasonable inflation standard should be based on the standard pressure marked on the tire and adjust the tire pressure appropriately according to the change in temperature. For example, in summer, the tire pressure should be 5% – 7% lower than that in winter. This is because the temperature is higher in summer, and the volume of the gas will expand after being heated, and the pressure will also increase accordingly. Therefore, the pressure should be appropriately reduced.
Taboo 10: Adding cold water suddenly when the water tank boils
When the engine experiences a boiling water tank phenomenon due to over – load operation, poor heat dissipation, or lack of water in the water tank, if cold water is added immediately at this time, it will bring a great uneven cooling effect to the cylinder head and the cylinder block, and it is very easy to cause the cylinder head and the cylinder block to crack.
Therefore, during use, once the water tank boiling is found, emergency measures should be taken immediately to stop the operation, let the cooling water of the diesel engine cool down naturally, and then conduct further inspection and maintenance after the temperature drops slightly.