What to pay attention to in the construction of well drilling machine pebble base (full analysis of well drilling technology in muddy pebble stratum)
Shaft drilling construction under complex geological conditions, especially in muddy gravel layer, requires comprehensive and scientific technical schemes and strict safety.
Geological exploration and site selection
Scientific site selection is the key to project success. The stratum structure is accurately identified through geological radar detection and drilling sampling and the GIS system is used for three-dimensional modeling to generate the stratum profile map, marking the areas where the gravel is enriched. At the same time, a perme is installed to monitor the change of groundwater level in real time, and the area with a slope greater than 5° and a permeability coefficient greater than 10⁻ cm/s is given priority. The Dijkstra algorithm is used to simulate the collapse risk, avoiding the strong permeable layer containing drift stones. For areas with a thickness of gravel layer greater than 8m, it is recommended to use the hole-spacing method for exploration, with the hole spacing controlled at 3 – 5 Metros.
Drilling process optimization
According to the characteristics of different strata, targeted combined processes are adopted. The impact-rotation composite drilling is equipped with a W-shaped drill bit diamond composite segments, which improve the crushing efficiency and the rate of return of drilling cuttings; the pneumatic down-the-hole hammer drilling is suitable for the dense layer with size greater than 150mm, with fast advance speed and small hole deviation rate; the mud wall protection technology uses a specific formula, which can effectively shorten the construction cycle a single hole.
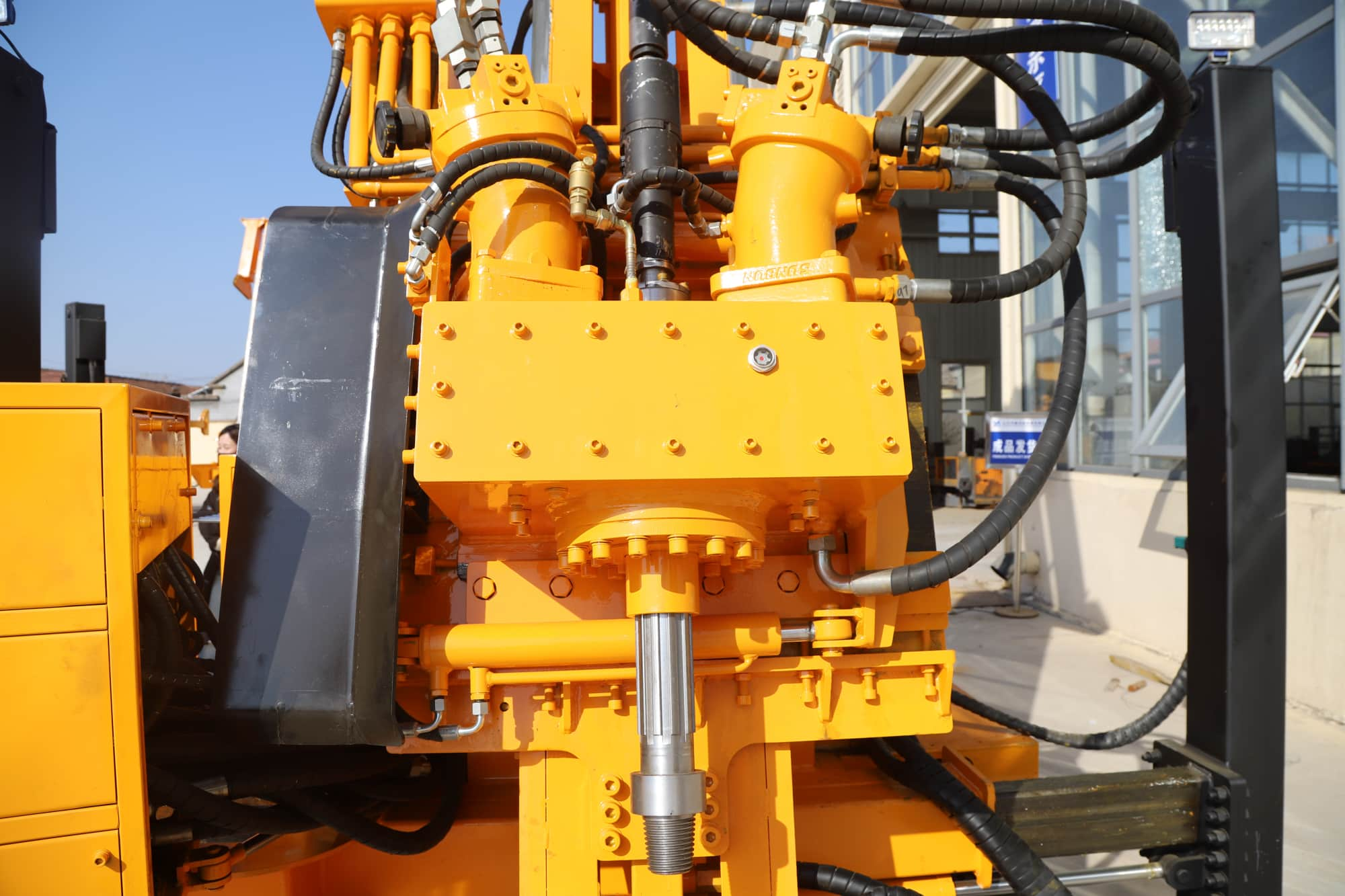
Drilling rig power head
Shaft wall protection technology
The graded wall protection scheme is implemented, with the shallow layer using the casing advance method, the middle layer using the-liquid grouting method, and the deep layer using the prefabricated concrete shaft wall. At the same time, the distributed optical fiber sensor is installed to monitor the strain temperature and seepage pressure of the shaft wall in real time, and an alarm is triggered when the strain exceeds 500με. In addition, 3D printing wall technology can achieve precise forming of complex curved surface structures and improve material strength.
Safety management system
Risk matrix management is applied, dividing the risk area into levels, focusing on the prevention and control of R4 level collapse risk, and configuring automatic pressure relief devices and emergency escape channels. Strict equipment maintenance standards are formulated, drill rod sealant grease and torque sensor accuracy are regularly replaced and detected. At the same time, emergency rescue cabins and high-pressure jetting obstacle removal equipment are equipped, collapse plugging simulation drills are conducted every month to ensure construction safety.