How impact-resistant design can extend the life of core drilling equipment and save maintenance costs
In harsh working conditions such as geological exploration and mining, equipment needs to withstand high-frequency vibration, sudden load impact and continuous pressure from complex terrain. As the core power transmission unit of the core drilling equipment, the impact resistance of the winch directly determines the overall life and operation stability of the equipment. In response to this industry pain point, Shandong Bangxin Equipo de Maquinaria Co., Ltd., relying on years of technical accumulation and customized design capabilities, deeply integrates the concept of impact resistance into the research and development and manufacturing of winches, providing users with solutions that are both durable and economical.
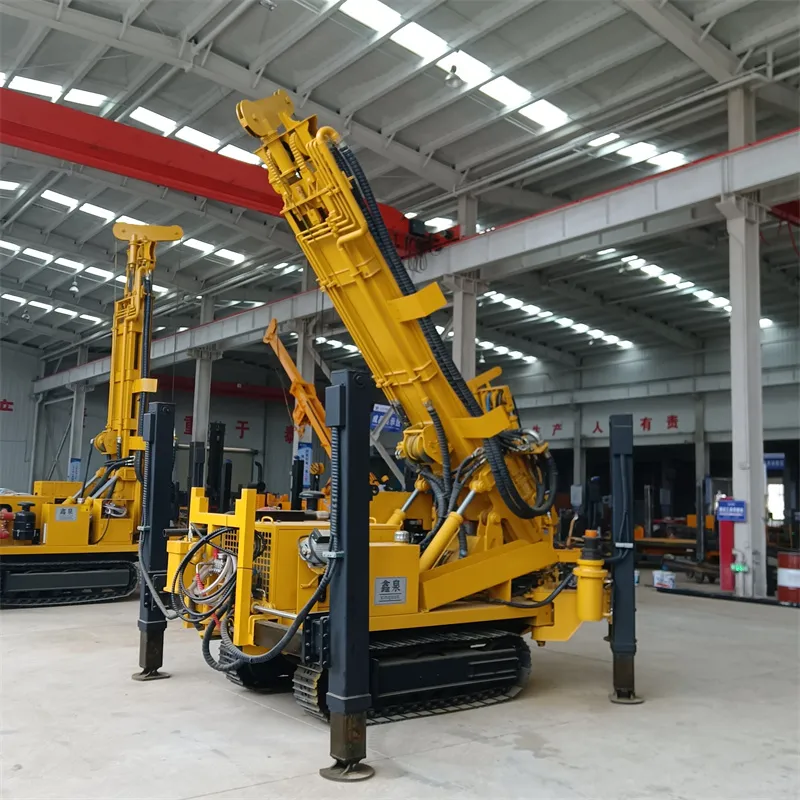
core drilling equipment
The core value of impact-resistant design: from passive maintenance to active protection
Traditional winches are prone to gearbox deformation, bearing wear and other problems due to instantaneous impact force under extreme working conditions. Frequent shutdowns for maintenance not only increase manpower and spare parts costs, but also affect the progress of the project. Adopting multi-dimensional impact-resistant design, from structural optimization, material upgrades to process innovation, a full-link protection system is constructed.
Box structure reinforcement: Through the overall casting process and reinforcement rib layout, the box rigidity is improved and the impact load is dispersed. For example, in response to the sudden drill jamming problem in deep hole drilling, a buffer cavity is added inside the box to effectively absorb the reverse impact force caused by the sudden stop of the wire rope and avoid damage to the gear set due to instantaneous overload.
Redundant design of key components: The main drive shaft adopts a stepped shaft diameter and a multi-bearing support structure to reduce the risk of eccentric load when subjected to radial impact; the clutch and brake are equipped with elastic damping modules to reduce the peak mechanical stress during the start-stop stage.
Dynamic balance adjustment: During high-speed lifting or heavy-load lowering, the lateral vibration caused by the swing of the wire rope is suppressed through counterweight optimization and inertia matching technology, extending the service life of the pulley block and guide wheel.
Customized technical path: Accurately adapt to complex working conditions
Different engineering scenarios have significant differences in the impact resistance requirements of winches. For example, mountain exploration needs to deal with the bumps and vibrations caused by frequent machine moves, while metal ore drilling faces impact loads caused by sudden changes in rock hardness. can provide users with the following customized services with its modular design platform and flexible production line:
Working condition-adapted structural solution:
In view of the characteristics of loose formations that are prone to hole collapse, a short-stroke, high-frequency winch is developed to reduce the vibration amplitude of the wire rope by reducing the single lifting height.
In hard rock drilling scenarios, a high-torque, low-speed model is provided, equipped with a dual braking system to ensure precise control and emergency braking safety under heavy loads.
Material and process directional upgrade:
Gear tooth surfaces are nitrided or sprayed with tungsten carbide coating to improve fatigue resistance and wear resistance.
The wire rope drum is embedded with a polymer shock-absorbing pad to reduce direct collision and friction between metals.
Intelligent monitoring expansion:
Optional vibration sensors and temperature monitoring modules can provide real-time feedback on the operating status of the equipment, predict potential fault points, and realize the transformation from “after-the-fact maintenance” to “preventive maintenance”.
Full life cycle cost control: a closed loop from cost reduction to efficiency improvement
The impact-resistant design is not only related to the durability of the equipment itself, but also significantly reduces the user’s full life cycle cost by reducing unplanned downtime and maintenance frequency:
Maintenance cost optimization: the enclosed gearbox and labyrinth seal structure can block dust intrusion and extend the lubrication cycle; the quick-release end cover design improves the efficiency of daily maintenance and reduces labor time.
Improved versatility of accessories: standardized interface design and highly interchangeable components (such as bearing seats and couplings) ensure that users can quickly replace them in an emergency to avoid the whole machine being shut down due to damage to a single component.
Maximized residual value: The impact-resistant reinforced winch has a higher value retention rate in the second-hand equipment market, especially for leasing companies or engineering projects with frequent transfers.
Empowering technological innovation with experience
As a professional manufacturer in the field of drilling equipment for many years, Shandong Bangxin has always paid attention to the reliability of winches.
At a time when competition for equipment homogeneity is intensifying, through the continuous iteration of winch impact-resistant technology, users can break through efficiency bottlenecks and cost dilemmas. Whether it is conventional geological exploration or ultra-deep hole drilling projects, we can respond to diverse needs with customized solutions, making each equipment a “profit engine” that can stand the test of time.